Siemens Develops a HIL Simulator for Wind Turbine Control System Testing
- markvasat
- Mar 13, 2023
- 4 min read
Updated: Aug 28, 2023
*As Featured on NI.com
Original Authors: Morten Pedersen, CIM Industrial Systems A/S
Edited by Cyth Systems

The Challenge Improving the automated testing of frequent software releases of Siemens wind turbine control systems as well as testing and verifying the wind turbine control system components in the development phase.
The Solution Creating a new real-time test system for hardware-in-the-loop (HIL) testing of the embedded control software releases of Siemens wind turbine control systems using NI TestStand, the LabVIEW Real-Time and LabVIEW FPGA modules, and the NI PXI platform.
Testing the Control System Software
A wind turbine system consists of several components including the rotor, gear, converter, and transformer used to convert kinetic wind energy to electricity.
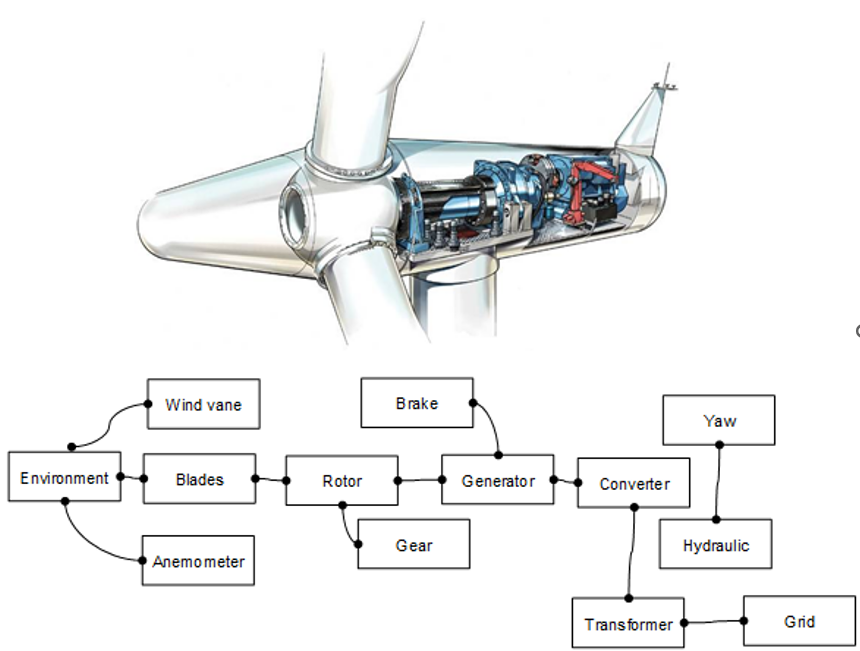
The control system interfaces with these components through hundreds of I/O signals and multiple communication protocols. The most complex part of the control system is the embedded control software executing the control loops.
Because our software developers regularly release a new software version for the controller, we need to test the software to verify that these releases will execute reliably in the wind park’s conditions. With every software release, we perform factory acceptance testing before the software can be used in the field. This new test system gives us the ability to automate this process.
Lessons Learned from the Previous System
Our previous test system was developed 10 years ago and based on another software environment and PCI data acquisition boards. The test system architecture and performance did not meet our new requirements for test time and scalability. It was difficult to maintain and did not have sufficient automation capabilities for efficient testing. It also lacked automatic test result documentation and test case traceability and did not provide the required remote control capabilities. In addition, the old HIL test environment did not support multicore processing, which prevented us from taking advantage of the computing power of the latest multicore processors.
Our Decision for Future Systems
After evaluating the available technologies, we selected LabVIEW software and PXI-based real-time and field-programmable gate array (FPGA) hardware to develop our new test solution. We believe this technology gives us the flexibility and expandability to meet our future technical requirements. Also, we have established confidence in the solution with the high level of service and quality of the products from NI.
Because we did not have in-depth development expertise for test systems in-house, we contracted the development to CIM Industrial Systems A/S in Denmark. We chose CIM because they had the test engineering capabilities and LabVIEW architects available.
A Flexible Real-Time Test System Architecture
The new test system simulates the behavior of the real wind turbine components by running simulation models for these components in the LabVIEW Real-Time system to supply simulated signals to the system under test.
Left: Siemens Wind Power Test System Architecture. Right: The host computer’s LabVIEW graphical user interface (GUI).
The software on the host computer communicates with the LabVIEW Real-Time target in a PXI-1042Q chassis over Ethernet. LabVIEW Real-Time runs simulation software that typically consists of 20 to 25 simulation DLLs executing in parallel. This solution can call user models built with almost any modeling environment such as the NI LabVIEW Control Design and Simulation Module, The MathWorks, Inc. Simulink® software, or ANSI C code. A typical execution rate of our simulation loop is 24 ms, leaving plenty of processing capacity to meet future expansion needs.
FPGA Boards for Custom Wind Turbine Protocols and Sensor Simulations
There are a lot of custom communication protocols used in wind turbines because of the lack of existing standards. Using an NI PXI-R Series FPGA-based multifunction RIO module with the LabVIEW FPGA Module, we can quickly interface with and simulate these protocols. In addition to protocol interfacing, we are using the device to simulate magnetic sensors and for accurate three-phase voltage and current simulations. The other FPGA board is connected to an R Series expansion chassis to further increase the system channel count. The ability to design software to run on an FPGA with the same graphical development environment used for real-time control was extremely helpful in increasing our productivity.
The Benefits of the New Test System
NI technology played a critical role in the improvements to the new Wind Power test system. The openness of the LabVIEW development environment, which allowed us to import third-party simulation models, combined with the tight integration of NI real-time and FPGA-based hardware, enabled us to quickly move from a concept to a functional prototype. LabVIEW’s ability to automatically take advantage of the latest multicore processors helped us maximize system performance, leaving plenty of processing capacity to meet future expansion needs. Finally, the highly customizable front panel enabled us to easily design an intuitive graphical user interface for our end users,
The new Siemens Wind Power test system is more modular than the previous generation, making it easy to improve, adapt, and further develop. The system under test can be quickly replaced without any changes in the test system architecture. The remote control capability and simple replication of the system gives us the flexibility to copy the system to other sites as our operations expand. Finally, the simulator provides an environment to effectively verify the new software releases and test special situations in our laboratory. It also gives us a tool to test new technologies and concepts we are working on.
Future Plans
LabVIEW’s graphical system design allows us to design modular software that can be easily scaled to meet the growing requirements of evolving wind energy technology. In the future, we envision expanding the simulation to multiple LabVIEW Real-Time targets to meet our future testing needs. We are also using NI TestStand to further automate test execution.
Original Authors:
Morten Pedersen, CIM Industrial Systems A/S
Edited by Cyth Systems
Comments