Nucor Refines Steel Recycling Using NI Hardware & LabVIEW
- markvasat
- Mar 7, 2023
- 3 min read
Updated: Aug 28, 2023
*As Featured on NI.com
Original Author: Dave Brandt, Nucor Corp
Edited by Cyth Systems

The Challenge Developing an automation system for a steel recycling facility that reduces the amount of energy consumed to comply with statewide energy regulations while improving the safety and efficiency of the plant.
The Solution Using National Instruments CompactRIO and the NI LabVIEW graphical programming environment to develop plant automation solutions to accurately measure the amount of energy required to recycle steel and improve facility safety.
Two out of every three pounds of steel is produced from previously used steel, making it the most recycled material in North America. Recycling steel consumes between 60 and 74 percent less energy than producing new steel from raw materials, which is equivalent to the amount of energy needed to power 18 million homes for one year.
Improving Steel Recycling
Steel companies are constantly refining their recycling operations to make the process more efficient and environmentally friendly. At Nucor, we place a high value on being stewards of our environmental resources, and to that end we have become the largest recycler of steel in North America. In 2005, we purchased the Marion Steel Company in Marion, Ohio, which gave us a location central to nearly 60 percent of the steel consumption in the United States. To maintain our high facility standards with this acquisition we immediately recognized the need to implement a facility automation system to improve the efficiency and safety of the plant.
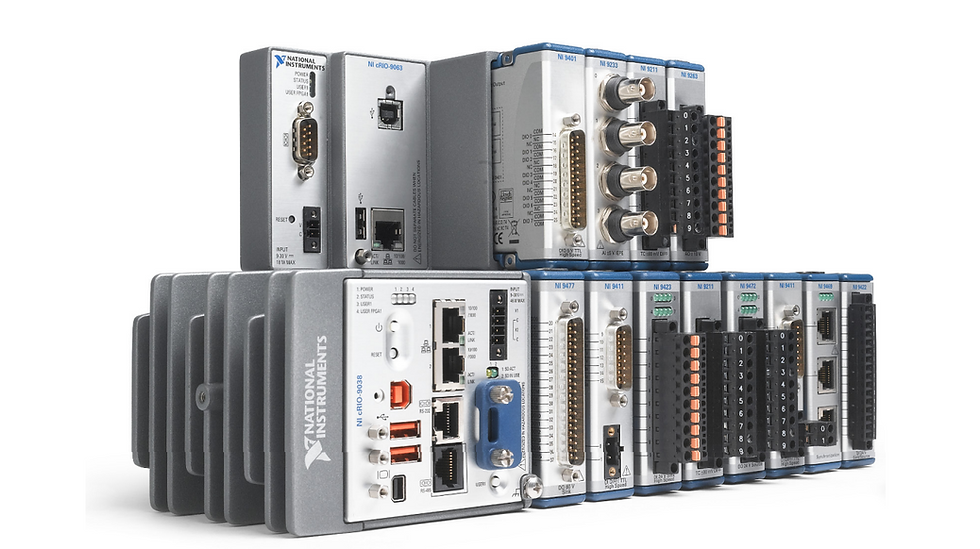
Reducing Energy Consumption with NI Software and Hardware
At the Marion facility, we manufacture a full line of rebar, sign supports, delineators, and cable barrier systems using recycled steel. During the steel recycling process scrap metal is heated in an electric arc furnace (EAF) and, depending on the type of steel being produced, a combination of elements is added to the viscous steel to create the appropriate steel alloy. This process requires large amounts of energy that vary significantly depending on the amount of scrap placed in the furnace. When we purchased the Marion facility, operators relied on estimates to determine the amount of steel placed in the furnace, causing the metal to be overheated oftentimes. This results in an unsatisfactory end product that must be recycled again, which costs the company time, money, and energy.

To reduce the number of reheats, we developed a low-cost scale and weighing system using LabVIEW and NI CompactRIO controllers that accurately calculated the amount of steel in each burn. Knowing the exact amount of scrap metal placed in the furnace allowed us to precisely calculate the amount of electricity required to heat the furnace. Prior to implementing this scale system, our steel measuring was hit or miss. We did not have a method of tracking the number of reheats prior to the implementation of the new system, however out of the more than 6,000 batches in 2007 after deploying the new system we only performed 10 reheats, which was far less than in 2006.
Eliminating Flicker with LabVIEW and NI CompactRIO
One risk involved in drawing the large amount of electricity required to heat the furnace for recycling is causing flicker on the power grid. Not only did we receive monetary penalties for using too much electricity, but the power grid flicker was an inconvenience to Marion residents. To reduce electricity consumption, we developed an online reactor in series with the furnace using the LabVIEW FPGA module and the CompactRIO platform that measures the amount of energy drawn from the power grid. If the furnace approaches the prescribed limit, the system can quickly change control methods to reduce the amount of power being drawn.
Improving Facility Safety with LabVIEW
One of our core values at Nucor is employee safety, thus another goal of our facility improvements was to make the Marion location a safer place to work. We determined we needed to upgrade the method for turning the EAF on and off. Before renovating the system, an operator had to manually pull the on/off switch, which made him or her vulnerable to injury if the fuse were to blow. A cRIO and an HMI were used to create a remote power switch that does not put operators in potentially dangerous situations.
The Benefits of Factory Automation
Using NI hardware and software, we developed a variety of automation systems that have greatly reduced the electricity we use and eliminated potential safety issues at our Marion, Ohio facility. The ability to have one platform handling all of our communication protocols (Ethernet, serial, Modbus, and EtherCAT), PID control loops, and sequencing algorithms saved us time and money. With LabVIEW’s graphical system design, we were able to further simplify our development by parallelizing all of our communication and control loops, which lead to increased system performance in addition to readable and maintainable code.
Original Author:
Dave Brandt, Nucor Corp
Edited by Cyth Systems
Comments