Photo Automation Pairs Software & Robotics to Boost Productivity
- markvasat
- May 25, 2022
- 3 min read
Updated: Oct 19, 2023
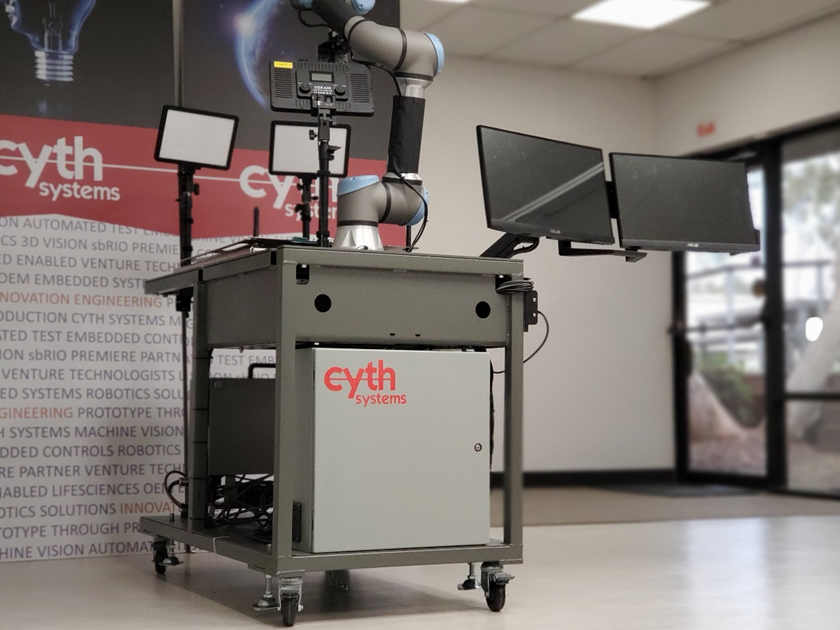
By integrating the latest technology in photography automation and leveraging the LabVIEW® architecture's power, Cyth has increased the speeds and capabilities of quality control’s latest tool, and has done so in a mobile design worth noting”.
-Test Engineer at Government Defense Contractor
The Challenge
Providing a high-performance, automated system which enables efficient photo documentation of selected products from any angle (including a full 360-degree scan), automating the camera positioning and settings, taking photos, and overlaying text to be bundled into project folders.
The Solution
Using LabVIEW software and a Collaborative Robot (CoBot), we delivered a system that automates the execution of predefined robot sequences that document selected image profiles of a subject efficiently while reducing labor costs.
The Story
For a large defense contractor in Southern California, one of the biggest challenges faced in their manufacturing environment was collecting and labeling images of finished assemblies as evidence of a completed build. From remembering which images were required, to manually copying files and labeling them correctly, this process was extremely time-consuming and susceptible to mistakes. With all the advances in modern technology this customer was certain that there must be a way to fully automate these photos but had trouble navigating the many options they found on the internet to decide how to begin.
The Traditional Approach
Human-performed quality control is still widely used in the global aerospace and defense industry. Common practices require technicians to take dozens of pictures of manufactured products using cameras and individually label images in post-processing software. This process is not only subject to the technician’s speed and job experience but is greatly slowed by the manual process of image labeling in popular image editing software. Previous systems required significant reprogramming and manual positioning for every new product to be photographed.
The Cyth Approach
To address these shortcomings, we built a machine and software that can manage and synchronize multiple parallel processes to adjust camera positioning, exposure, and image labeling. First, an operator places the desired part on the imaging platform. Next, the operator creates robot positioning tasks using the configuration interface that requires no programming. The software, developed using LabVIEW, allows the operator to define positions, camera settings, and labeling options without doing any reprogramming. This enables an operator to specify an unlimited number of images at any angle or location relative to the desired part. Then operating in a synchronized flow, the system captures images of the part adjusting auto-focus and auto-exposure in real-time.
The machine was built using a heavy-duty SwiveLink wheeled cart which gives the system the mobility to be positioned wherever needed. Our engineering team installed an off-the-shelf robot mounting system that gives the cart the ability to hold the CoBot arm. The images are acquired by the Canon EOS 5D Mark IV attached to the robot’s manifold allowing for the 360-degree acquisition of images. Two adjustable monitors are situated on the side of the cart that make up the operator's workstation and allows the operator to control all CoBot movement and images taken.

Overcoming the Obstacles
One challenge our engineering team faced was determining the best way to tag and append the images taken by the camera. There are nine fields of text overlaid on every image and finding the most efficient way to automatically add text within a flexible and consistent program was a challenge that required careful software architectural implementations. Our team went about achieving this by first identifying which of the text fields were constant vs. changing. Then, after having the program fill the text fields the footer was appended to the original image which allows it to be stored in runtime memory. It is essential for all images taken to be appended accurately with their respective footer as an overlay to the image, and our approach allowed for all images to be tagged in a way that did not slow processing speeds.
Achieving the Outcome
As a result of the image automation cart’s development, the client has been able to greatly increase the efficiency of their quality control process at a lower cost. Not only did we accommodate the client’s needs throughout the project, but were able to meet all requirements within time and budget constraints. After the product was delivered our team was able to send support engineers to make the installation and bring-up of the new machine seamless as well as provide training for the client on how to use the new equipment in their quality control process.
Technical Specifications
· 1 x Olympus Controls UR5e Robot
· 1 x SwiveLink Mobile Table Cart for Robot Workstation
· 1 x Seedit Robot License
· 1 x Canon EOS 5D Mark IV
· 1 x Canon EF 35mm f/2 IS USM Lens
· 1 x Intel NUC Skylake Compact Fanless Computer

Comments