Measurement Automation System for Electromagnetic Medical Device
- markvasat
- Feb 2, 2023
- 3 min read
Updated: Aug 28, 2023

Electromagnetic Medical Device Measurement Automation System
The Challenge
A medical manufacturing company approached us with the need for a system to automate the measurement of an electromagnetic industrial test fixture built to test medical devices in volume.
The Solution
Using NI PXI hardware, LabVIEW software, magnetometers, and an ergonomic design we built the customer a turnkey solution that automated the electromagnetic measurements of their medical device and test fixture.
The Story//The Cyth Process
Our client has an industrial test fixture that incorporates a Helmholtz coil, to produce a region of a uniform magnetic field.
When there is a change in the magnetic field of the Helmholtz coil there is a current induced because of the detected magnetic waves.
This concept was incorporated into the client’s design of their industrial test fixture to test their product, an electromagnetic medical device.
Our system provided the power to pulse their device, their industrial fixture read the induced current, and our system acquired and analyzed the measurements.
To do so our fixture housed 2 NI PXI Chassis with high-speed I/O, 2 industrial PCs, and two Fluxgate Magnetometers.
A magnetometer measures the direction, strength, and relative change of a magnetic field which we acquired using high-speed PXI analog inputs.
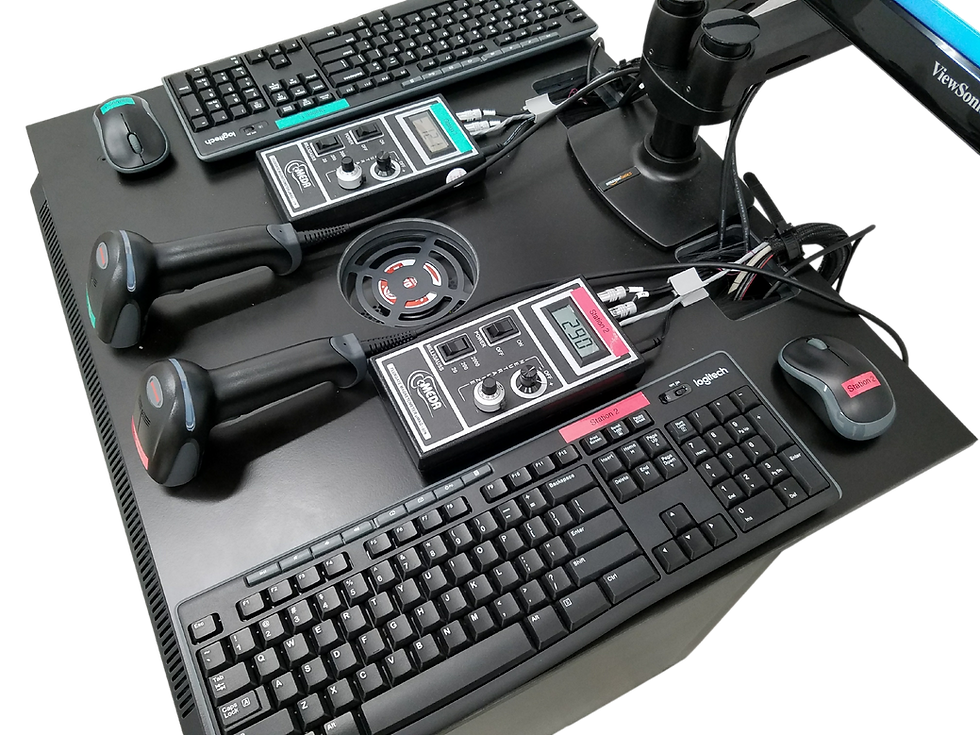
System Highlights
Our engineering team designed the system to measure and quantify the electromagnetic waves the client’s medical device emitted.
Our system’s design simultaneously interfaced with two client industrial test stations. This enabled a singular operator to run two stations.
A LabVIEW user interface and software architecture provided an operator with simple controls which logged acquired data directly to a database via Ethernet.
We precisely controlled the device’s provided power to measure consumption and used a data acquisition device to generate waveforms to measure changes in the device’s electromagnetic pulses (EMF).
System Order of Operations
An operator loads the EMF medical device into the client’s industrial test fixture, scans the barcode, and connects the required wiring.
The operator begins the test on the LabVIEW user interface (UI) menu.
Our system uploads firmware to the client’s device and performs a low-level power on before testing the client’s device at different power levels (to simulate battery power).
The device is pulsed, and our system automatically reads and acquires the electromagnetic signals using the NI PXI high-speed analog I/O. The readings are then measured using the fluxgate magnetometer.
The percentage error between control and measured magnetic field readings is performed by LabVIEW algorithms and deems the device a pass or reject sample on the user interface.
The measured data is then uploaded by our system into the client’s database via Ethernet.
Once the test is complete the UI prompts the operator to load the next sample and repeat the process.
Delivering the Outcome
Using NI PXI hardware, LabVIEW software, magnetometers, and an ergonomic design we built the customer a turnkey solution that automated the electromagnetic measurements of their medical device and test fixture. Our measurement fixture’s ability to interface with two client test stations simultaneously increased the efficiency of their in-house quality control. A single test was completed in approximately 5 minutes which enabled the client to increase the repeatability of their testing process. The use of LabVIEW enabled our measurement control architectures and high-speed data acquisition. The project hardware and software were completed within 8 weeks and within the client’s project budget and timeline requirements.
Technical Specifications
1 x PXI 4-slot Chassis
1 x NI PXIe-6341 Multifunction DAQ Analog Input/Digital I/O
1 x NI PXI-4110 Programmable DC Power Supply
1 x NI PXI-2564 16 SPST Relay Module
2 x Dell Embedded Industrial PC
2 x Meda Fluxgate Magnetometers
2 x Barcode Scanners
1 x Rugged Mobile Cart
Comments