Kraft Foods Uses Intelligent Machine Fault Detection for Easy Mac Manufacturing Line
- markvasat
- Jul 14, 2023
- 4 min read
Updated: Aug 15, 2023
*As Featured on NI.com
Original Authors: Alok Sarwal, Handeportal Systems
Edited by Cyth Systems
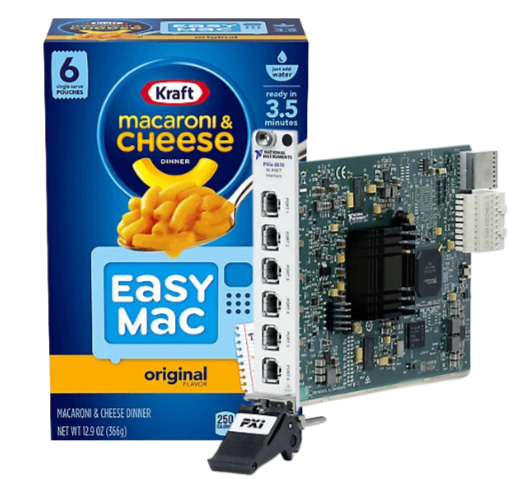
The Challenge
Developing advanced fault-detection diagnostic and servicing tools to maximize production line performance and reduce equipment downtime.
The Solution
Using NI LabVIEW software and the PXI hardware platform to provide a data acquisition solution for the diagnosis of manufacturing line health and performance.
Machine malfunctions, slowdowns, and other inefficiencies are problems that plague all production lines. The speed of these machines makes it difficult to isolate problems and the origins of machine jams and other unexpected stoppages are often misinterpreted by line operators and can go unrecorded and uncharacterized. One problem or malfunction leads to another in a multi-stage system, creating a domino effect and making the original issue difficult to identify. Additionally, problems may be irregular or develop over a long period of time, making it hard to determine what went wrong.
To solve this problem, researchers at the worlds leading food and beverage company developed the Remote Observer of Manufacturing Equipment (ROME), a solution that actually reconstructs the events that lead to system failure. Like the black box flight recorders used on aircraft, ROME is a diagnostic tool designed to support food and beverage machinery. It combines signal data and video using multiple cameras and provides an integrated time-stamped data bundle.
ROME is the result of our Advanced Manufacturing Systems (AMS) approach developed by researchers to address the problem of reduced equipment efficiency by creating advanced diagnostic and servicing tools to maximize line performance and reduce downtime. ROME provides all the necessary instruments for collecting adequate video, digital, and analog data and the tools required for analyzing this data to diagnose serious problems such as high-speed equipment stoppages, slowdowns, or production-line inefficiencies.
The ROME system includes at least two high-resolution color video cameras that are scene specific and acquire data at 30 to 60 frames per second. ROME can accept up to 265 digital inputs (optically insulated input voltage from five to 250 VDC/VAC). ROME also accepts 16 analog signals of 4-20mA (12-bit resolution). The system has a real-time clock and is designed with no outputs to eliminate the possibility of influencing the operation of a machine’s control system.
High-speed frame grabbers give ROME the power to capture up to 10 seconds of video once a digital trigger, or fault, is detected for post-analysis. ROME can continuously capture data for up to 80 independent 10-second “events” with a 10-second buffer, meaning the previous 10 seconds of data is preserved at any given time. Also, ROME can monitor machinery equipped with any type/brand of programmable logic controller (PLC). The original ROME system has been upgraded to the ROME-2. Handeportal Systems developed both applications.
A prototype of ROME-2 was developed, tested in a laboratory, and installed on actual production lines. This system continues to benefit the various production lines and is now considered a mainstream fault-detection and fault-diagnostic tool that increases overall equipment efficiency.
For this system, we chose off-the-shelf hardware components from National Instruments and were able to develop the prototype system for about $20,000. The original development was done by consultants with expertise specifically in real-time programming of data acquisition and vision-equipped robotics. Since a physical interface can disrupt the production line, a custom interface was developed for ROME-2. To provide a noninvasive mechanism for ROME, the data-acquisition signals are transmitted in a multiplexed manner to detect high-speed digital triggers from high-resolution LEDs on plant control equipment.
Finally, adding a FireWire® hard drive supports a hot-swappable storage resource that can archive numerous sequences of fault triggers and allows the plant floor staff to hot-swap the drive and perform data analysis and fault detection. The overall plan for this tool is to provide significant cost savings by reducing downtime and supporting the concept of predictive maintenance.
The LabVIEW graphical system design environment was also a key component of this application because it allowed for rapid development of the real-time detection and analysis platform. Because NI LabVIEW can easily target various operating systems, we were able to prototype within the Microsoft Windows environment and deploy on the real-time OS within NI PXI embedded controllers. COTS hardware from National Instruments offered standards-based hardware that supported deployment in ruggedized manufacturing environments. Moreover, the technical support provided by field engineers and product experts helped resolve problems specific to this application.
Post Processing
Meticulous post-processing of the events captured by ROME is handled by an X86 Microsoft .NET application-based program called DataViewer. Its user-friendly GUI permits step-by-step analysis of video frames synchronized with signal data from the event data buffer.
Multiple resolutions are available, and users can define a set of signals of interest to view in the time window. This application is distributed to all analysts at a particular plant. While users can utilize offline analysis to understand why a machine is not operating at full capability under certain conditions or operates differently at different time periods, they can also use the online collection to compare a baseline system running at optimal performance and one that indicates faulty behavior. Such reference-based, or finger-print, comparisons provide an efficient means of predicting faults that could otherwise be quite difficult to determine.
Original Authors:
Alok Sarwal, Handeportal Systems
Edited by Cyth Systems
Comments