Converting Legacy Control Systems to NI’s Cutting Edge PXI
- markvasat
- Jul 24, 2023
- 3 min read
Updated: Aug 15, 2023
*As Featured on NI.com
Original Authors: Nathanael Mackley, Mantaro Product Development Services
Edited by Cyth Systems
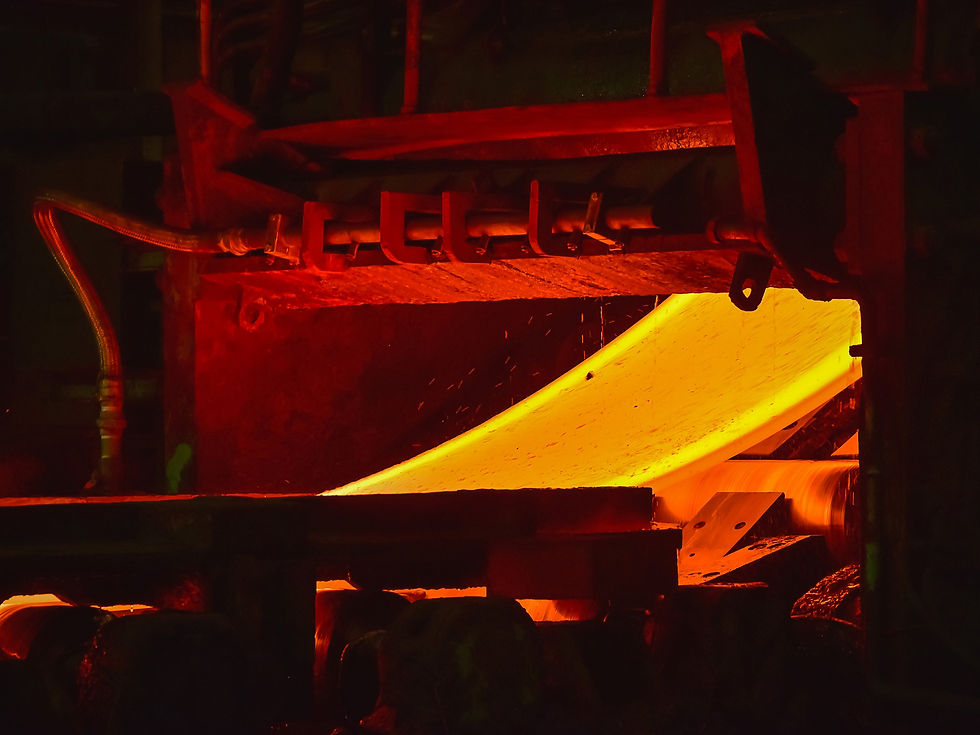
The Challenge
Replacing the legacy (out of date) control system of six hot rolling mill in a steel production facility.
The Solution
Using the NI PXI platform with LabVIEW software to create a modern, flexible control platform that minimizes deployment costs, minimizes production downtime, and maximizes code reuse.
A major steel manufacturer in North America needed to replace a critical control system for six hot rolling mill stands. The original hardware had reached obsolescence, and key components were unavailable or priced at premium rates. With a potential loss of thousands of dollars per minute of downtime, it was imperative to keep the production line running and avoid costly delays and downtime. The steel manufacturer selected Mantaro Product Development Services to implement a control system upgrade program to replace the legacy hardware with a modern platform while porting as much of the existing code as possible.
Hot Rolling Mills: A Demanding Environment
Every aspect of a hot rolling mill requires awareness of the hazards involved, well-engineered components, and affordability. This is compounded when the mill is operational every day for 24 hours a day with no room for downtime outside of scheduled maintenance and service operations. Capital investments are large with support requirements extending well past 10 or even 15 years for the control and monitoring systems.
This particular mill had been in operation for nearly 15 years. The control system was built around the Multibus II platform and made extensive use of custom and proprietary hardware solutions from the original systems integrator. Electrical isolation was required to protect the Multibus platform from plant-wide and local ground loops and electrical surge. The new hardware platform would be required to meet or exceed the existing isolation performance. The legacy hardware was generally reliable, but typically required as many as 15 minutes from power up to reach run state. Reducing this start-up time was highly desirable, but zero tolerance for equipment and process failures stemming from unreliable hardware meant that changes to the state machines would be viewed as undesirable. The operational ANSI C code ran on the iRMX real-time OS. Each of the major control processes required its own processor, and each processor was operating at or above 80 percent utilization. The fastest processes were operating at 1 ms cycles and often depended on inherent latencies in the Multibus platform. Moving to a modern control platform presented an opportunity for significant application improvement.
Left: System Diagram of Hot Rolling Mill System, Right: NI PXI installation.
Hardware Implementation
Our hardware engineers adopted a “plug and play” approach to system design. The entire upgrade system was located in a self-contained, standard 19 in. cabinet, permitting a single, common design as a drop in replacement for each successive control system in the entire mill facility. The signal I/O interconnect between the legacy and upgrade systems was a bundled bus design. This simplified the design of the cable and allowed the documentation to be reduced in complexity, thereby removing several man-weeks of labor costs. The signal I/O interconnect used the legacy interface with adaptation to the upgrade control system wiring schema occurring in the new cabinet. This allowed the installation of the upgrade system to add only a single point of change to the operational system during the development and test phases.
Software Implementation
Our software engineers tried to reuse as much of the original code during the development process while adhering to the mantra of “do not break anything you touch.” The original code was ported from multiple processes in multiple processors to a single thread in a single real-time core of the new Intel Core 2 Duo based controller. Final breakdown of the code included 80 percent of the original code and approximately 20 percent of new code to support the PXI platform, a different RTOS, and several new features. The new architecture permitted the real-time processes to run serialized and at a synchronized 1 ms cycle.
*As Featured on NI.com
Original Authors: Nathanael Mackley, Mantaro Product Development Services
Edited by Cyth Systems
Comentarios