CompactRIO Controls World’s Largest Fuel-Cell Hybrid Train
- markvasat
- Feb 6, 2023
- 4 min read
Updated: Aug 28, 2023
*As Featured on NI.com
Original Authors: Tim Erickson, Vehicle Projects LLC
Edited by Cyth Systems
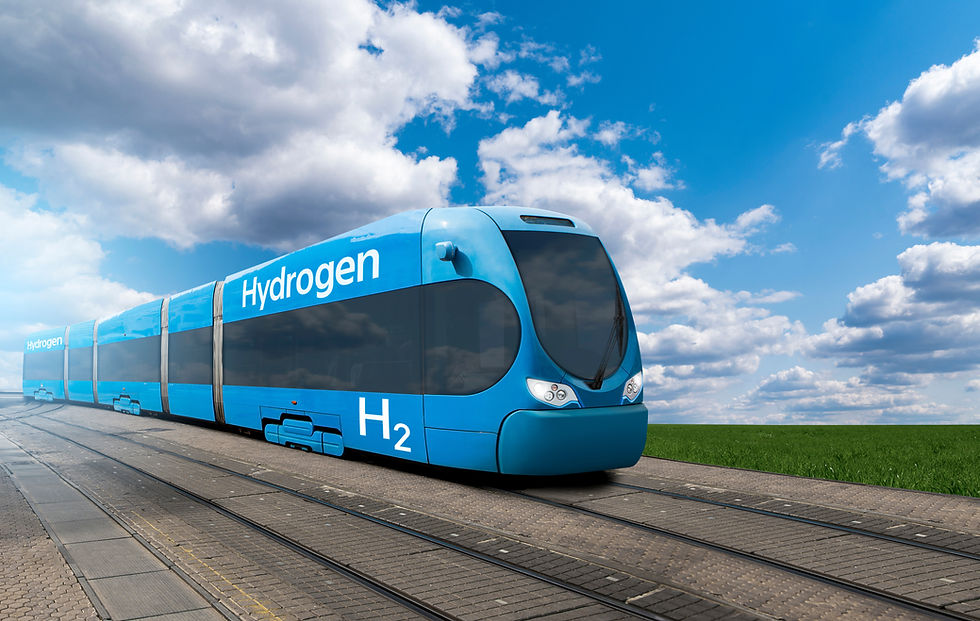
The Challenge Controlling the operation of a 250-kW fuel-cell hybrid locomotive.
The Solution Using an NI CompactRIO controller to monitor and control the safety and operation of a fuel-cell locomotive and controller area network (CAN) bus to communicate the engine status to the operator via a touch panel programmed with NI LabVIEW software.
The prime mover of a traditional switch locomotive is a diesel engine between 1 and 2 MW driving an alternator that supplies power to the traction motors and locomotive auxiliary systems. These traditional switch locomotives require a high-power diesel engine, which typically is not fuel-efficient and has limited emission control. Subsequent design iterations of switch locomotives have transitioned to a hybrid-electric design, which reduces the overall emissions and fuel consumption because the engine can be downsized while the battery stores energy for high-power transients.
However, a large source of diesel particulate pollution in urban areas still comes from diesel-powered locomotives in rail yards. To help alleviate this pollution, a North American public-private partnership is prototyping a fuel-cell hybrid switch locomotive for urban rail applications and replacing the diesel engine with a 250-kW net fuel-cell power plant, creating the world’s largest fuel-cell hybrid locomotive.
Vehicle Projects LLC of Denver, Colorado, engineered the control system for the fuel cell using a CompactRIO embedded controller and LabVIEW graphical design software. Our goals are to reduce air pollution in urban rail applications, including yard switching associated with seaports, and to serve as a mobile backup power source for critical infrastructure during military base grid failures or civilian disaster relief operations.
Fuel Cells and Hybrid Power Trains
Fuel cells are electrochemical power devices that directly convert the chemical energy of a fuel into electric power. The cells produce electricity and water from hydrogen fuel and oxygen, which is the reverse process of water electrolysis. While fuel cells share principles of operation with batteries, they differ in that the electrochemically active materials, hydrogen and oxygen, are stored or available externally and continuously supplied to the device rather than stored in the electrodes. They are periodically refueled, like an engine, rather than recharged electrically. Like batteries, individual cells are grouped together into “stacks” to provide the required voltage or power.
A fuel-cell hybrid power train uses a fuel-cell prime mover plus an auxiliary power/energy-storage device to carry the vehicle over power peaks in its duty cycle and recover kinetic or potential energy during braking. For steady-state operation, the continuous net power of the prime mover must equal or exceed the mean power of the duty cycle. Preliminary research has shown that a hybrid-switch locomotive can reduce capital and recurring operation costs.

Figure 1. Top: NI Compact RIO 4 Slot Chassis.
Bottom: NI CompactRIO 8 Slot Chassis.
Designing a Control System Using CompactRIO
We faced several design and integration challenges while developing the large hydrogen fuel-cell vehicle including weight, packaging, and safety considerations. Harsh operating conditions, especially the shock loads that occurred during coupling to railcars, required highly rugged component systems. Additionally, the fuel-cell control system is needed to communicate with the existing commercial vehicle controller to interpret operator demand and adjust fuel-cell power plant parameters to meet the power requirement. The CompactRIO embedded controller provided an ideal form factor to meet these specifications with the right I/O combination for this application. This programmable automation controller (PAC) managed and executed all power plant functions and continuously monitored the performance and safety of the hydrogen storage and fuel-cell power systems.
Software Architecture Based on LabVIEW
A CompactRIO embedded controller running the LabVIEW Real-Time and LabVIEW FPGA modules controls the fuel-cell power plant operation. The user monitors the control system via a touch panel installed in the locomotive cab. The control application consists of modular control algorithm VIs that communicate with each other and the field-programmable gate array (FPGA) I/O system using a tag-based architecture so that we can refer to each I/O point by the assigned name within the LabVIEW application. Each tag has properties associated with it including alarm limits, scaling (converting from voltage to engineering units), and events such as when the user wants it to log to a disk. We implemented a programmable logic controller (PLC) mentality into our PAC-based system.
Developing the Perfect Control Platform with LabVIEW and CompactRIO
We chose LabVIEW and CompactRIO because the NI C Series modules with integrated signal conditioning helped us implement fast monitoring of the various I/O points while connecting to a wide range of specialty sensors such as flowmeters and pressure sensors.
Additionally, we performed complex control algorithms beyond simple proportional integral derivative control at very fast loop rates. Some of our control algorithms included mathematical models that we implemented with LabVIEW, which we could not have developed using less flexible environments such as a PLC platform. Furthermore, we achieved the fast loop rates that we required because we had the ability to place some of the control algorithms on the field programmable gate array (FPGA).
Technical Specifications
LabVIEW 2020
NI CompactRIO 8-slot Chassis
Author Information: Tim Erickson Vehicle Projects LLC
Comments