CompactRIO Monitors the Main Gearbox of a Bucket-Wheel Excavator
- markvasat
- Feb 3, 2023
- 3 min read
Updated: Aug 25, 2023
*As Featured on NI.com
Original Authors: Pawel Pawlik - AGH University of Science and Technology
Dariusz Dabrowski - AGH University of Science and Technology
Edited by Cyth Systems
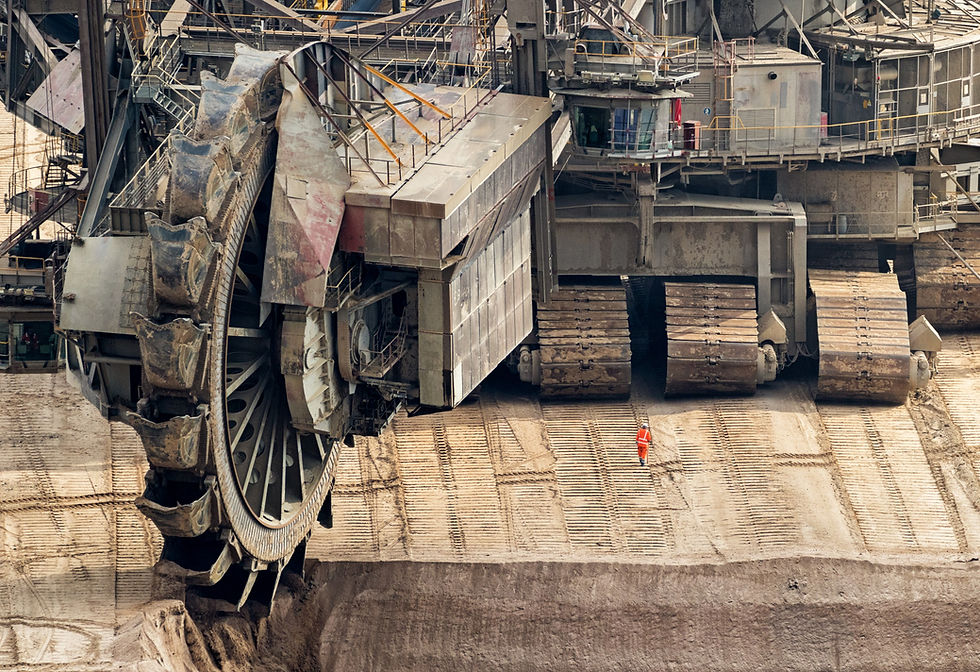
The Challenge Monitoring the planetary gearbox of a bucket-wheel excavator power transmission system to proactively predict parts failures before they occur.
The Solution Using NI CompactRIO hardware and LabVIEW software to develop a rugged condition monitoring system to track multiple gearbox parameters using high-speed analog and digital I/O.
The Story//Process
Machine condition monitoring in mines is economically critical. The costs of unplanned downtimes can quickly cripple a mine’s revenue due to the reduction in production and costs of repairs. Machine condition monitoring systems help minimize down time by predicting failures before they happen.
In the Konin opencast mine (Poland), we developed a machine condition monitoring system for the bevel planetary gearbox, which is part of the power transmission system of the bucket-wheel excavator KWK-1500s (see Figure 1).

System Hardware
Due to demanding industrial and environmental conditions the machine condition monitoring system had to be resistant to shock, vibration, and temperature. It also needed to ensure failure-free operation with the guarantee of diagnostics tasks. Due to these requirements, we chose the NI cRIO-9022 controller and NI cRIO-9114 chassis for our system.
To being, we used the NI CompactRIO and the NI 9234 C Series modules to acquire vibration signals. Accelerometers we installed on the gearbox casing measured the signals. The CompactRIO controller facilitated communication with the programmable logic controller via Modbus TCP/IP protocol. As a result, the user could read excavator operation conditions such as oil temperature, oil pressure, power, and rotational speed remotely from controller registers.
The CompactRIO device was connected to the industrial panel computer IPPC-6192A by TCP/IP protocol. The system used a touch panel computer for data logging, results presentation, and communication with PC computers that had access privileges.
Figure 2. Left: A conveyor in an open-cast coal mine.
Right: I/O vibration data points located along the frame of the excavator.
System Software
Using LabVIEW, we configured the FPGA to perform parallel data acquisition. Afterward, the system sent data to the real-time controller via a first-in-first-out (FIFO) memory buffer, which was configured in the DMA mode.
The main application ran on the real-time controller as a multithreaded structure. The structure featured four basic threads: acquisition, ACQ programmable logic controller (PLC), analysis, and communication with the panel PC. The system listed the threads from the highest priority to the lowest. With the multithreaded structure, we could add functionality to the system, such as acquisition analysis or communication, without interfering with the existing program code.
Figure 3: Left: Window of data analysis.
Right: The software structure on the real-time controller.
In the structure, the communication with the PC panel thread was the master thread because it sent commands to the other threads and was responsible for communication with the panel PC. The industrial panel computer used Secure Digital (SD) disks for data storage where the raw signals and all calculated estimates were archived. The system used Technical Data Management Streaming (TDMS) binary files for data logging and acquisition parameters storage.
The touch panel PC connected to the mine’s internet remotely for data transmission from the excavator to the PCs. Users with privileges could remotely control system parameters.
Diagnostic Signal Analysis
The planetary bevel KPB 190-214 transmission gear (nominal power 630 kW, transmission ratio 190 and input shaft rotation 990 rpm) is especially designed for drive systems of bucket-wheel excavators in open-pit mining. The gearbox is divided into four parts from a diagnostics point of view: input shaft, bevel gear, first planetary gear stage, and second planetary gear stage. Figure 3 shows the front panel of the PC application.
Rugged, Flexible System
Overall, we developed a machine condition monitoring system for the bevel planetary gearbox on the bucket-wheel excavator KWK-1500s located in the Konin opencast mine (Poland). By using NI CompactRIO hardware, we were able to build a rugged system capable of withstanding harsh industrial conditions (vibration) and environmental conditions (weather). We remotely controlled the system parameters and observation of registered data via the mine’s internet by VPN connection. Using LabVIEW’s software architecture, we were able to capture continuous data logging, develop new diagnostics procedures, after verification of new algorithms, incorporate them into the system.
References
1 National Instruments, NI LabVIEW for CompactRIO Developer’s Guide, 2012
2 http://www.flsmidth.com, 19.09.2012
Author Information Pawel Pawlik - AGH University of Science and Technology
Dariusz Dabrowski - AGH University of Science and Technology
Edited by Cyth Systems
Comments