Compact Data Logger for Train Performance Validation
- markvasat
- Feb 24, 2023
- 3 min read
Updated: Aug 28, 2023
*As Featured on NI.com
Original Authors: Arunkumar Manoharan - Apna Technologies & Solutions Pvt Limited Sriram Iyer - Apna Technologies and Solutions Pvt Ltd
Edited by Cyth Systems
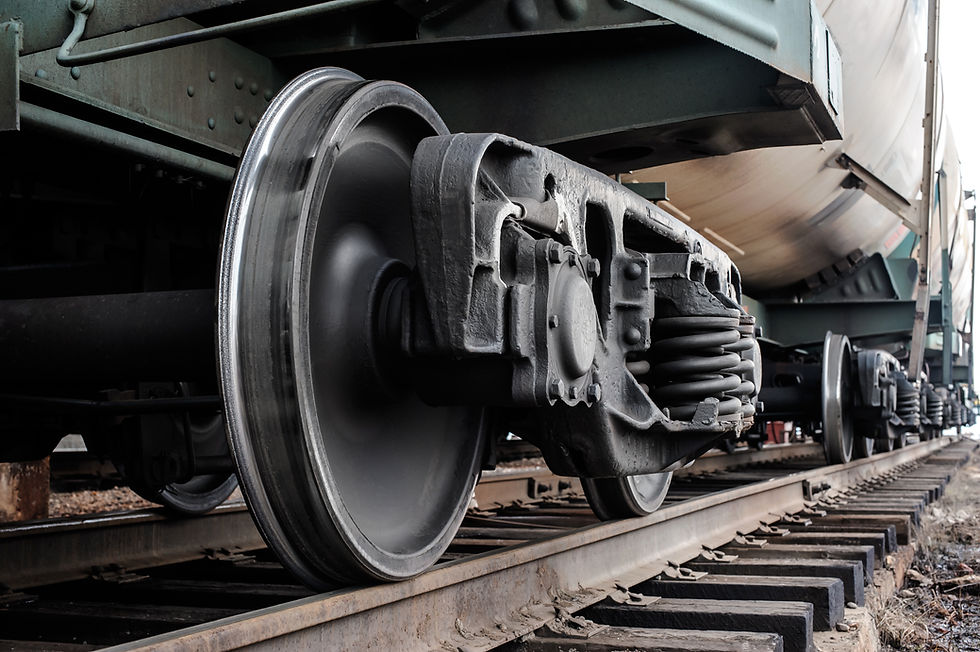
Background and Process
The Research Design and Standards Organization of the Ministry of Railways of India uses validation trials to set standards for Indian railway conditions. During validation trials, we test trains with certain load and speed criteria on a new or existing railway line. We also test locomotives and railway vehicles with modified designs under different track conditions.
Knowing parameters such as twist, gauge, alignment, and unevenness is critical for gauging the performance of a train when running along a track. We needed to create a product to digitize, store, and analyze the data of the train while it is running meanwhile maintaining flexibility in sensor connection and appropriate signal conditioners. The logger needed to withstand the high vibration and electromagnetic interference common in the railroad environment.
We used NI CompactRIO hardware and LabVIEW software to create the Apna Versatile Data Acquisition System (apnaVDAS) data logger. The CompactRIO controller, chassis, and respective modules gave us the input and output configuration we required for the system. We developed a LabVIEW application to detect the configuration of the modules and load the appropriate user interface and analysis. The required sensors including strain, accelerometer, displacement, pressure, temperature, and speed were integrated with ease. These sensors help us in real-time to measure the impact loads caused by wheel defects, and measure axle speeds, and help us gauge the dynamic load for all the wheels. The application featured in our Wheel Impact Load Detector (WILD) creates a live track chart with measurements from sensors and marks corresponding to events (locations such as curves, straight lines, bridges, rise, fall, and stations) recorded by the imaging sensor and corresponding manual entries. Online and offline analysis software analyzes recorded information. The apnaVDAS data logger has a modular front panel and built-in signal conditioning modules. The front panel provides signal-specific LEMO connectors for ease of handling and is optimized to acquire measurements in the rugged and demanding conditions of a running train.

Measurement Architecture
We connected sensors mounted on different measurement points in the oscillograph car or test vehicle to the apnaVDAS with a shielded cable. The other end of the shielded cable features LEMO connectors. The connector size and mating notches are different for different signal types to avoid problems in the field.
After we configure the test and initialize the CompactRIO controller, the NI cRIO-9014 controller collects the data from other CompactRIO modules at 100 S/s and transfers the data to a rugged laptop.
Data Logger
We used an 8-slot NI cRIO-9104 chassis that we can configure to meet any test requirement. LEMO connectors interface from the field sensor to the enclosure front panels. The connectors feed required excitation voltage and current via sensors through customized module printed circuit boards. The data logger features battery backup for up to four hours in case of an emergency. The enclosure complies with the IP65 rating and is rugged enough to work in train-running conditions.
Software
We used LabVIEW to develop the apnaVDS software. Customers can configure the display and sensor scaling parameters in the apnaVDAS software per test requirements. They can save and retrieve data for similar trials.
Conclusion
We used LabVIEW and CompactRIO to develop a reliable, rugged data logger with field-configurable plug-and-play I/O modules to meet stringent transportation requirements. We successfully have conducted several railway trials across India to expand our customer base to Mumbai Metro, Chennai Metro Rail, and Jaipur Metro amongst many more. LabVIEW software and CompactRIO hardware provided a deterministic platform that reduced our development time and increased the reliability of our system for rugged environmental conditions.
Original Authors:
Arunkumar Manoharan - Apna Technologies & Solutions Pvt Limited Sriram Iyer - Apna Technologies and Solutions Pvt Ltd
Edited by Cyth Systems
Comments