Automating a Robotized Production Cell Using NI CompactRIO
- markvasat
- Jul 26, 2023
- 5 min read
Updated: Aug 15, 2023
*As Featured on NI.com
Original Authors: Walid Lachiheb, Sagemcom Tunisia
Edited by Cyth Systems
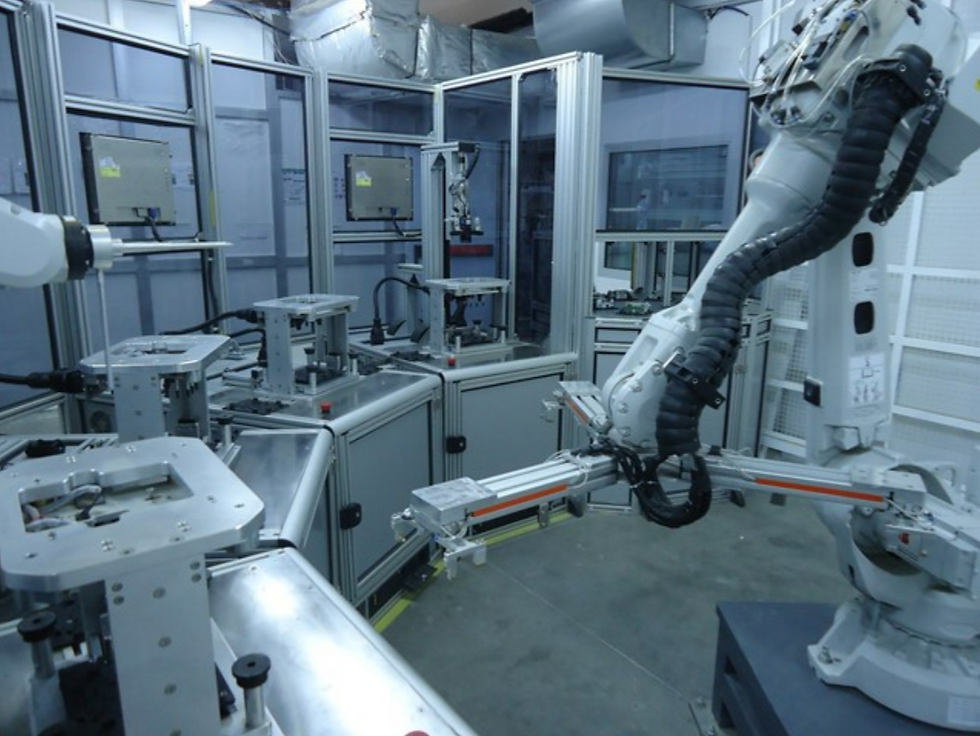
The Challenge
Developing a new test bench design to test power meters with the flexibility to interoperate with automation devices and robotics arms through industrial protocols and adaptability to various product lines.
The Solution
Combining the benefits of the CompactRIO computation power and its easy interoperability through LabVIEW programming to create a rugged real-time testing solution and operating with robots and performing synchronized testing and monitoring safety with respect to robotic machine safety regulations.
Project Overview
Sagemcom, a European leader in telecommunications and energy, has been steadily growing since becoming a PRIME alliance member for sponsoring smart meters with PLC-based communication for energy meters and smart grids. We maintain our leadership and provide a high-quality production level and volumes. Therefore, Sagemcom Technology NRJ, an NI Alliance Partner located in Tunisia, has been awarded a new project. This group is responsible for the design and development of turnkey test bench solutions for Sagemcom’s plants and partners all over the world. The new project is to increase actual production volume in a Tunisia factory and ensure a contractual engagement with a customer for line fluidity equal to 99 percent.
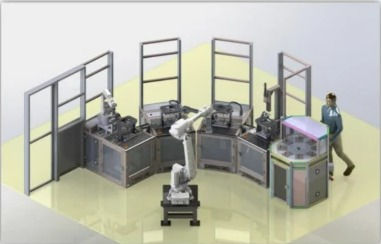
During the vision inspection, we must guarantee the functionality of the LCD and indicating LED of the product. In the past, operators performed tests through manual inspection. We have automated through PC-based automatic test benches using Vision Builder for Automated Inspection. To perform this test we need to interface with camera, automation devices, products through Ethernet communication, and safety controller through Modbus TCP/IP.
Concerning the HIPOT test, we must inject 3.2 KV into a product and check its immunity to this high voltage. We need to interface with the accommodating instrumentation through RS232 interface and respect a precise time frame for the leakage current’s measurement. The purpose of the PLC test is to simulate the behavior of the product after field deployment while communicating with the data concentrator in the power line protocol. We need Ethernet/IP communication with a special instrument for signal modulation analysis. During functional testing we have to acquire and analyze communication signals and then interact with a product’s button while acting with a cylinder. This test is quite sensitive due to the accuracy needed to interact with some buttons that have limited access.
Duplicating this architecture does not ensure contractual first pass yield (FPY) engagement due to the troubles observed with PC-based solutions (crashes, application bugs, and virus vulnerability). In addition, a budgetary improvement request has been introduced to limit investment on development budget and global solution costs. Considering all these criteria, we faced a challenge and our focus turned to thinking of a constructive way to:
Enhance FPY and robustness of test benches
Reduce development time and save money
Reduce test time and increase volume to save on our investment
Reduce handling time to provide a better throughput and avoid operator-related delays
Add technical value to the project (hiring a more qualified support team, taking our company from a pure manufacturer to special machine developer, and maintaining our manufacturing capabilities).
Reducing Handling Time and Providing Better Throughput
After considering the challenge, our first step was to determine an efficient way to reduce handling time and deliver better accuracy while positioning products into test fixtures. Simulations concluded that a robotic cell configuration with a central robot for handling products and an additional smaller robot for performing functional test would work well. We interconnected four test benches and synchronized them to ensure optimal process flow. Even though we selected robots for better handling time, we faced an additional challenge. What is the best way to program them for an efficient predictive algorithm and setting priority to robot handling?
CompactRIO for More Robustness and Reduced Testing Time
The objective to reduce test time without neglecting robustness significantly impacts this challenge. Through this condition we should identify the most suitable hardware architecture that can provide the highest level of robustness for each cell’s node. In fact, the project income was to guarantee that the adopted architecture could permit safe data exchange between each node in a way that the product could be functionally tested and inspected through vision. We also have to provide a necessary algorithm to set the priority for positioning the robot arms while communicating through DeviceNet protocol and supervising all safety sensors to prevent any security violation. We had to consider that after performing primary studies, we identified a large number of digital I/O and a variety of instruments that communicate through RS422 protocol, Ethernet/IP, Modbus TCP/IP, and even DeviceNet.
Thus we had to find a control platform that could:
Ensure vision processing
Ensure parallel processing operations and advanced programming capability
Support industrial protocols
Exchange process information as safely as possible
After analyzing the available solutions for machine control, we turned our focus to two possible compliant architectures: either using programmable logic controller platforms or the CompactRIO system from NI. We chose CompactRIO because of the calculation power of its processor and FPGA, its support of a large number of industrial protocols, and its easy interoperability through LabVIEW programming. The CompactRIO platform offers built-in vision capabilities and supports camera connectivity over USB and Gigabit Ethernet, which are key differentiators. This system leads to a fully integrated solution and we can save money by avoiding costly smart camera solutions coupled to programmable logic controllers. The CompactRIO platform can also accelerate embedded vision applications through the Vision Development Module, which includes many image processing functions that can run on both a real-time processor and an FPGA.

The possibility of using CompactRIO to perform true parallel operation through its FPGA offered a way to reduce test time by paralyzing acquisitions and test sequence.
We adopted the cRIO-9030 for our project due to its powerful dual-core Intel Atom E3825, its high-value Kintex-7 FPGA, and the possibility of handling an embedded user interface through its MiniDisplay port, which could help us save investment by using additional PCs for deporting HMI. We chose CompactRIO to overcome a technical issue we observed in the PC-based architecture. A sensible burst measurement can cause a high level of false failure. Even with a costly digital multimeter deployed into that previous architecture, we always faced a high level of line rejection. In fact, we have to perform an RMS measurement accurately for a burst signal having an average amplitude of 700 mV modulated at 50 KHz. This burst allows the meter to synchronize with the power line communication network.
Project Outcome
Due to the high interoperability of the CompactRIO system and the native support for true parallelism and precise time looping through FPGA, we reduced test time by 21 s, which led to 17 percent productivity growth. This represents a higher throughput and a significant return on investment. We also reduced the number of controllers since we used one cRIO-9030 for all test benches instead of a single industrial PC for each machine, as we had done in the previous machines. This saved 50 percent on controller cost.
Original Authors:
Walid Lachiheb, Sagemcom Tunisia
Edited by Cyth Systems
コメント