ATE for the Calibration & Measurement of Automotive Display Instruments
- markvasat
- Jul 5, 2023
- 2 min read
Updated: Aug 15, 2023
*As Featured on NI.com
Original Authors: Tamás Balogh, Robert Bosch Kft
Edited by Cyth Systems
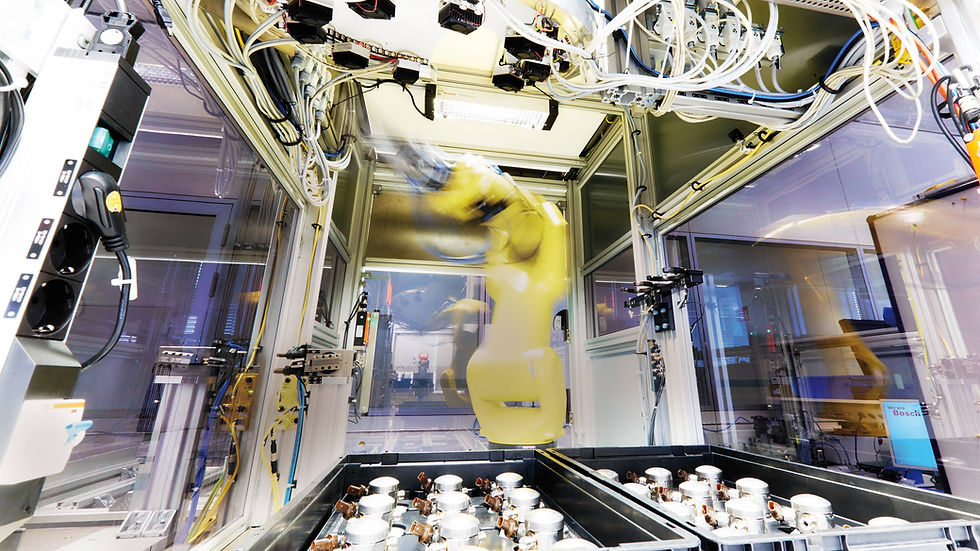
The Challenge
Reducing the time required to test the automotive display instruments Bosch provides to automotive manufacturers worldwide while maintaining high test for accuracy and measurement repeatability.
The Solution
Automating the test of Bosch automotive display and measurement instruments using a vision system enclosure housing a robot arm that uses NI data acquisition hardware and LabVIEW software to automate high-speed measurement and testing and does so in real-time.
As one of the world’s leading suppliers for the automotive industry, Bosch Car Multimedia has proved its OE competence in display and control elements for vehicle and driver assistance functions. These include display surfaces within the driver’s range of vision and the extensive networking of individual systems via the vehicle’s bus system.
From the mechanical point of view, the system has to fulfill several requirements. Instrument clusters have displays that are measured and calibrated during testing. To implement this correctly, the measurement equipment has to measure from the center of the display. To make sure each piece of measurement equipment has a chance to measure the display, we must line up the equipment on a horizontal bar. Then we insert the product with the display into a product-specific jig, which is inserted into a swivel table that rotates the product to each piece of measurement equipment along the horizontal bar.
LabVIEW architecture block diagram
From the electrical and software point of view, the biggest challenge is to handle a lot of special measurement equipment with different hardware interfaces.
Based on our experience and the equipment’s existing drivers, we decided to use LabVIEW as the platform to control all equipment. With LabVIEW, we can insert all existing drivers, create new ones, and address all the communication protocols used in the automotive industry. After developing the necessary software components, we use TestStand to create and run the test sequences. Because our system is designed to communicate with, control, and measure the products, our colleagues can read a short user manual to create their own test sequences and run them on the test station.
Results
We achieved the following results with our new automated test system based on the NI platform:
Before, one measurement took about 4 minutes and now it takes about 10 seconds.
The average number of measurements we make is 40. Before, that took about 160 minutes and now it takes about 6.6 minutes.
We gained test repeatability and accuracy improvements.
The easy-to-use test system reduces the development time of additional test sequences.
Original Authors: Tamás Balogh, Robert Bosch Kft
Edited by Cyth Systems
Comentarios